Using Historical Data for Accurate Construction Estimates
Accurate construction estimates aren’t built on guesswork, they’re grounded in the hard lessons of past projects. In this guide, we’ll demonstrate how tapping into your historical cost records can turn broad assumptions into data-driven precision. You’ll learn how to assemble and standardise past job metrics, apply analytical techniques to uncover cost and productivity trends, and weave those insights into every new bid.
By the end, you’ll see exactly how a disciplined, history-backed approach helps your team bid confidently, minimise overruns, and win more contracts.
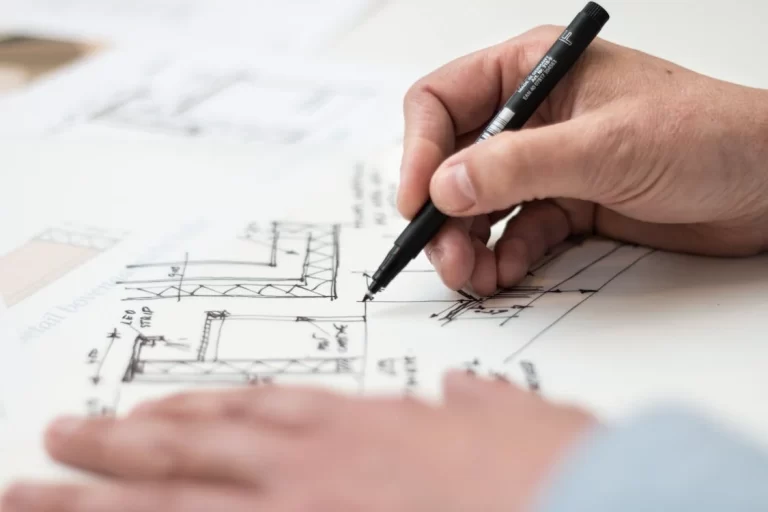
The Role of Historical Data in Accurate Estimates
Relying solely on generic cost guides or rule-of-thumb multipliers often leads to under- or over-pricing. Historical data provides real-world benchmarks, actual labour hours, material usage, equipment costs, site-specific allowances, that reflect the unique challenges of your geography, subcontractors, and supply chain.
By comparing similar past projects, construction cost estimators can spot patterns in productivity and unit costs, uncover hidden contingencies, and calibrate allowances for waste, rework, and unforeseen conditions. This foundation is the direct answer to improving estimate accuracy: build bids on your own project history rather than broad industry averages.
Collecting and Organising Historical Data
Before analysis, you need reliable inputs:
- Standardised Job Sheets
Ensure every project captures the same core metrics: crew hours by trade, material quantities by spec, equipment hours, subcontractor invoices, and change order histories. - Digital Cost Database
Migrate records into a central spreadsheet or database labelled by project type, size, location, and complexity. - Quality Control
Regularly audit entries for completeness and consistency, mis-entered labour rates or missing site allowances skew trend analysis. - Granular Breakdown
Segment data into work packages (e.g., formwork, welding, mechanical installation) so you can compare apples to apples when estimating a new job.
A well-organised repository is the backbone for any modern contract estimating services offering reliable, repeatable bids.
Analysing Data for Insights
With clean data, apply these methods:
Trend Analysis
Chart unit costs over time to spot inflationary pressure or productivity gains. For example, if pipe-welding labour rates rose 5% annually, factor that increase into new estimates.

Regression Modelling
Use simple linear regressions to correlate project size or complexity (e.g., total tonnage) with labour hours or materials. This statistical approach uncovers non-linear effects—perhaps larger jobs enjoy scale economies, while very small jobs incur setup inefficiencies.
Benchmarking Against Industry Averages
Compare your internal metrics to published data to validate if your historical rates fall within expected ranges, adjusting where you find consistent variance.
Identifying Outliers
Flag projects with extreme cost deviations. Investigate: Were these due to atypical site constraints, client-driven scope changes, or data entry errors? Excluding or appropriately weighting outliers refines your forecasting accuracy.
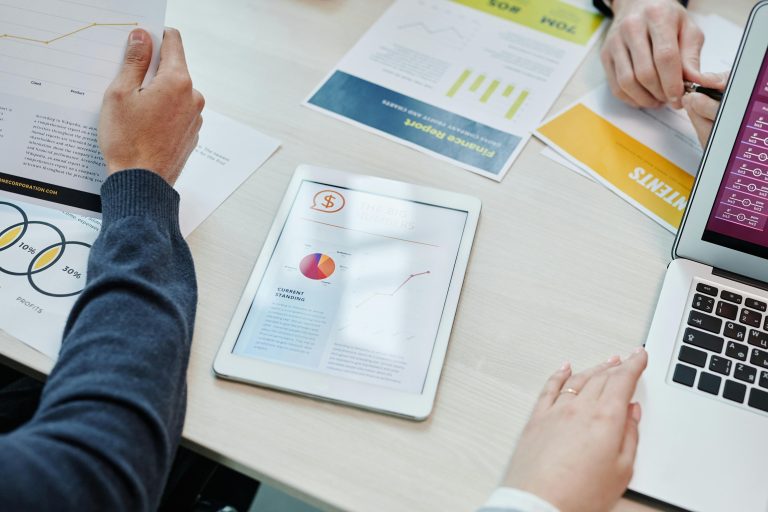
Implementing Data-Driven Estimates
Armed with insights, follow a structured estimation workflow:
- Baseline Projection
Start with unit rates derived from your historical database for each work package. - Adjust for Current Conditions
Escalate material costs based on recent supplier quotes; update labour rates to reflect prevailing union or market wages. - Site-Specific Modifiers
Apply location factors (e.g., remote access, traffic management requirements) informed by past jobs in similar settings. - Risk Allowances
Allocate contingency percentages grounded in the frequency and cost impact of change orders observed historically. - Peer Review
Have another estimator or foreman validate assumptions against both the historical database and current site intel.
This disciplined approach ensures that every bid leverages proven data while remaining responsive to present circumstances.
Leveraging Technology and Tools
Modern estimating platforms can simplify data-driven workflows:
- Cloud-Based Cost Libraries
Tools like Procore, PlanSwift or Sage Estimating let you build, share, and update central cost libraries accessible across teams. - Takeoff Automation
Integrate 2D or 3D model takeoff software to automatically quantify materials and link them to your calibrated unit rates. - Analytics Dashboards
Visualise cost trends, productivity metrics, and bid-win rates to continuously refine your historical database. - API Integrations
Connect project management and accounting systems so actual costs flow back into your estimating library in real time, closing the feedback loop.
By adopting these technologies, you empower your construction cost estimators to work faster and with greater confidence.
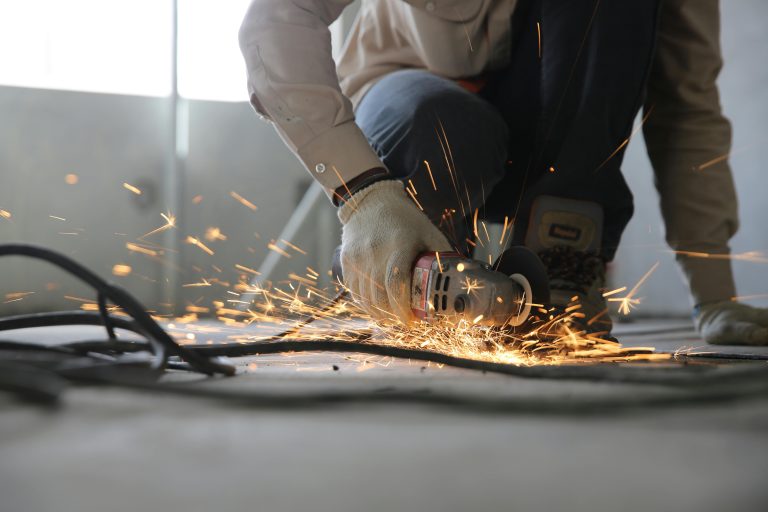
Best Practices for Ongoing Improvement
To keep your data and processes sharp:
- Regular Updates
Refresh your historical database monthly or quarterly—don’t let stale numbers undermine your bids. - Cross-Functional Collaboration
Involve site superintendents, project managers, and procurement specialists to validate data and share observations about cost drivers. - Document Lessons Learned
After project close-out, hold wrap-up sessions to capture unique challenges or innovations that may influence future estimates. - Scale Your Library
As you expand services, build dedicated sub-databases so specialised estimators can tap tailored benchmarks.
Adherence to these practices turns estimation into a strategic advantage rather than a necessary chore.
Partnering with Smart Industrial
Unlocking the full potential of historical data isn’t just about spreadsheets and stats—it’s about transforming your bid process into a data-driven engine of accuracy and profitability.
At Smart Industrial, our services are built on decades of on-site experience and a continuously refined cost library that reflects real conditions across New South Wales. We provide end-to-end support to ensure your next project is estimated, and executed, with absolute confidence. Contact Smart Industrial today to see how our data-backed approach to construction estimates can give you a competitive edge.